Performance characteristics:
This machine is a four-column powder forming machine. The electrical control system is controlled by a computer system. The time can be adjusted according to the processing situation, and both automatic and manual working modes can be realized. The working pressure and the travel range of the slider can be adjusted according to the process requirements, and two process modes of fixed pressure and fixed stroke forming can be completed. The fixed pressure forming process has the action of maintaining pressure and delaying automatic return after pressing.
Technical Parameters
Working pressure: 100T | Ejection force: 100T |
Motor power: 11KW | Maximum diameter of lower die: 500mm (customizable) |
Loading height: 200mm (customizable) | Maximum tableting diameter: 500mm (customizable) |
Output: 4-5 times (single color) | Maximum working pressure: 25MPa |
Maximum stroke of upper punch: 200mm | Ejection stroke: 250mm |
Structural Overview
This machine consists of two parts: the main machine and the control structure, which are connected through pipes and electrical devices to form a whole. The main machine includes the machine body, main cylinder, etc.; the control mechanism includes the hydraulic pump station (power system), electrical box, mobile operating table, etc. The structure and function of each part are described as follows:
(1)Machine body
This machine consists of an upper crossbeam, a slider workbench, columns, locking nuts and adjusting nuts, a machine base, etc. The slider
is equipped with a guide sleeve, relying on four columns as the main frame to make the slider move up and down. The upper crossbeam and the workbench are fixed with locking nuts at both ends. The machine accuracy is adjusted by adjusting nuts and locking nuts fixed to the upper crossbeam.
The slider and the main cylinder piston rod are connected by flanges for users to install molds. The column and piston rod of the machine are made of 45# steel, which can extend the service life of the machine after treatment.
(2)Cylinder
The machine has two upper and lower cylinders and one auxiliary cylinder.
The upper and lower cylinders are made of 45# integral forged steel. The upper cylinder body is fixed to the upper beam by the cylinder port shoulder and lock nut. The lower cylinder body is fixed to the lower beam by the cylinder port shoulder and lock nut. The lower end of the piston is connected to the slider with a connecting flange and bolts. The piston head is made of cast iron for guidance. The piston head is connected with an imported YX-type sealing ring in opposite directions. An O-ring is installed on the piston rod to divide the cylinder into two oil chambers. A guide sleeve is installed on the cylinder, and an O-ring is installed on the outer ring of the guide sleeve. It is locked with the flange and bolts to ensure the sealing of the cylinder port. A dust ring is installed on the cylinder port flange to ensure the dustproof of the piston rod. The auxiliary cylinder is responsible for feeding.
(3)Hydraulic station
The hydraulic pump consists of an oil tank, an oil pump, a motor, a two-way cartridge valve, an oil filter, and an air filter.。
一.The oil tank is a Q235 steel plate welded joint, with a pressure gauge and a remote overflow valve installed at the front end for observing and adjusting the pressure; a liquid level gauge is installed on the side of the oil tank to observe the liquid level; an oil suction filter is installed at the oil pump suction port to ensure the normal cleanliness of the pump hydraulic system; refueling can be carried out by opening the upper cover, and a cleaning port is provided on the side of the mailbox. The oil tank can be cleaned by removing the cover; an oil drain port is provided at the junction of the side and bottom of the oil tank.
二.The fuel tank is a steel plate welded structure, shot peened and rust-proofed, with a cleaning window on the side of the tank. The oil mark, air filter, valve manifold, etc. are arranged in order above the fuel tank cover.
三.The main hydraulic pipelines are connected by flanges and are equipped with reasonably arranged seismic pipe clamps to prevent vibration and leakage of high-pressure pipelines. The pipelines are pickled and passivated before installation to ensure the cleanliness of the oil.
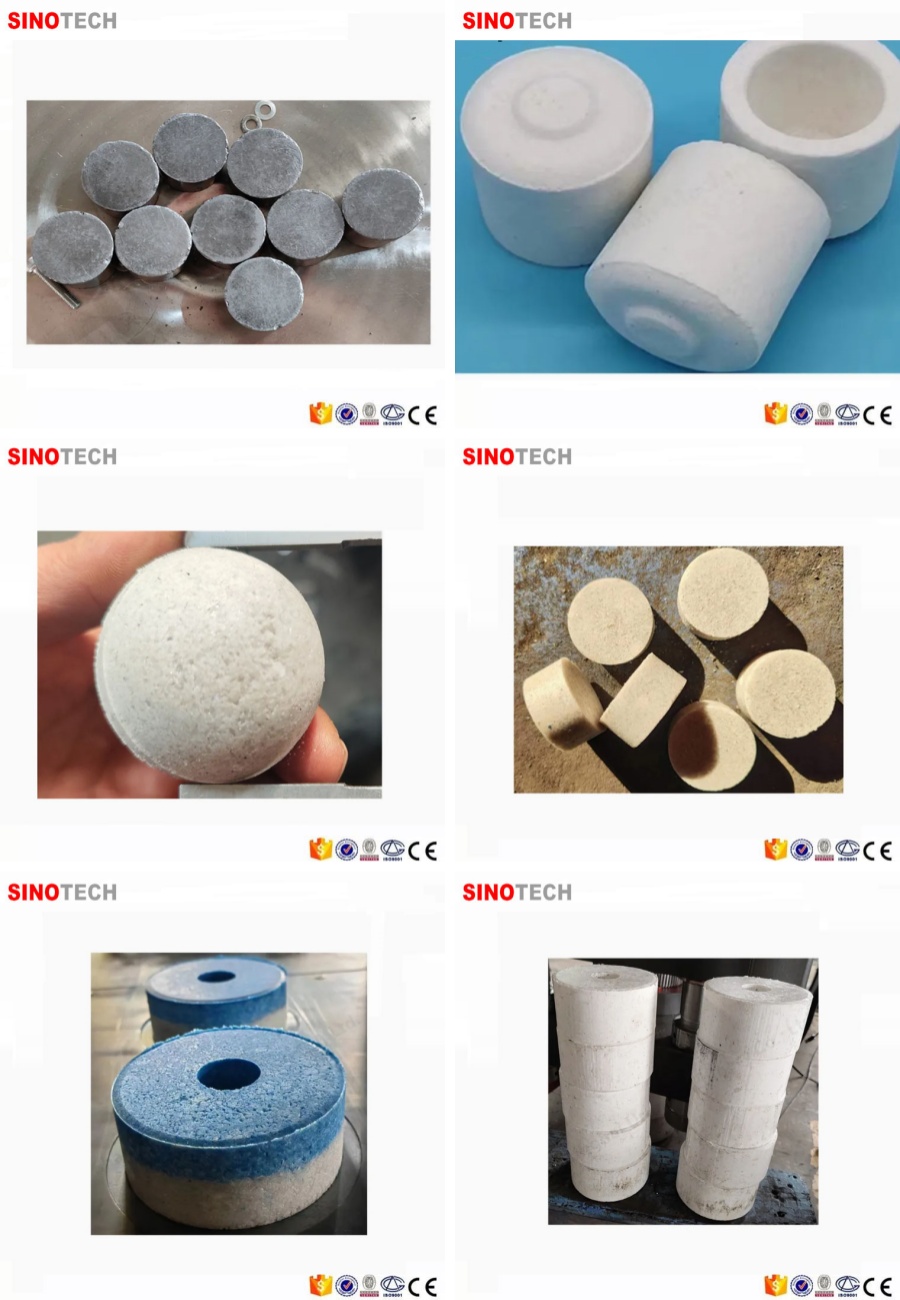
Overview of Hydraulic System
The hydraulic system consists of energy conversion devices (pumps and cylinders) and energy delivery devices (oil tanks, pipelines), etc.
With the help of the control of the electrical system, the slider is driven to complete various action cycles. The hydraulic system adopts a dual pump oil supply system. An oil filter is installed at the oil inlet of the pump to prevent impurities from entering the hydraulic system and ensure the normal operation of the oil circuit.
The system has an oil temperature and oil level display, an air filter, a cleaning window on the side, and a screw plug for draining oil and sewage at the bottom.
This machine has adjustment, semi-automatic, and fully automatic working modes to choose from. The adjustment action can be adjusted by adjusting the corresponding button to get the click action of the slider.
Electrical control system
This machine is equipped with an independent electrical control cabinet and a touch screen.
The electrical control cabinet is mainly used to install power control components. Such as controlling the main power supply and motor start control components.
Operating system
The hydraulic system consists of pumps, valves, cylinders, oil tanks and pipelines. With the help of the control of the electrical system, the movements of each component can be driven to complete smoothly.
In order to ensure the product qualification rate of the pressed parts, this machine is equipped with adjustment action and semi-automatic cycle process action mode: adjustment action, inching operation is to press the corresponding button to get the required corresponding action, and adjustment operation is used to adjust the pressure, speed, and stroke of various valves for adjustment or installation of molds;
Safety protection
Standstill and emergency buttons: When an abnormality occurs, press the "Standstill" button to stop the action, and press the "Emergency Stop" button to stop the motor from running.
Configuration List:
Control transformer | BK380V/220/24V/16V |
Intermediate relay | Omron |
Circuit breaker | DZ47 |
Touch screen | Vylon |
PLC | Xinjie |